Wiring diagrams:
For
military Nortons, a number of 6V
negative (-) earth
systems have been used based on the existing equipment or the
operational requirements of the time at which they were applied. It was a
relative simple system and used
by most of the contemporary British motorcycle manufacturers. Some used
Miller equipment.
Lucas supplied both the ignition and lighting system components in the form of the
Magdyno, a combination of a magneto to feed the spark plug and Dynamo to
deliver power to the (many times troublesome) lighting system.
On all military Nortons, the lighting switch and Ammeter (if applied) were mounted into a small panel which in turn
was screwed onto the top backside of the Lucas DU142/DU42 headlamp shell. On civilian
motorcycles, owners had an option to mount the electrical equipment into a
panel mounted on top of the petrol tank. These motorcycles were then
provided with a completely closed headlamp shell type Lucas D142.
"Lucas
invented darkness" or Lucas "Prince of darkness" are some of
the many adjectives for the products of Lucas manufacture. Many of the
problems were caused by bad maintenance or by the harsh environment into
which the bikes were operated.
There have been 2 basic electrical equipment systems where the later
version was used in four different electrical wiring schemes.
Electrical equipment variation one:
The first machines of 1936 did not have the luxury of the later introduced
CVC (Compensated Voltage Control), but had to do with a switch to have the
dynamo disconnected, at half charge or at full charge. A wire coil resistor
mounted to the headlamp switch panel was used to "burn-off" the excess of power when
the system worked at "half charge". This system is also
described as the "three brush dynamo" system.
The system worked using a switch with "OFF", "C", "H" and "L" positions.
When the battery was full, the rider could set the system to "OFF", in
which case the dynamo was disconnected from the system. When the battery
became discharged, the rider had 2 choices, half charge "C" for riding
without the lights or lights on and full charge, switch position "H".
The dynamo for this system was provided with an electro-magnetic cut-out
which connected the dynamo to the charging circuit as soon as the dynamo
voltage rises above that of the battery and disconnected the dynamo from
the charging circuit when the dynamo voltage dropped below the battery
voltage, to prevent the battery discharging itself through the dynamo.
Only the 1936 WD machines used this system as
the CVC was introduced in 1937 which led to the "Norton 1937
specification" annotation which was the standard for all machines after
that.
Electrical equipment variation two:
The CVC (Compensated Voltage Control) took the worry of proper
charging from the rider and is basically a electro-mechanical regulator. It
regulates both Voltage and Current by two coils working as electromagnets
activating electrical contacts when either Voltage or Current exceeds a
certain maximum value. The dynamo did not have the cut-out as mounted on
the previous machines. The
regulator (CVC) was factory mounted on the right hand upper rear chain
stay above the tool box. In military use, these boxes sometimes changed
position to the opposite left hand side upper rear chain stay. Ease of
access to the wiring was probably the driver for this "field
modification".
Regulators working on the same principles were used throughout the
motoring industry of that time until replaced by the electronic versions
of today.
The wiring diagram changed over time based on operational requirements.
Initially the basic civilian scheme was applied using a 3
position headlamp switch
(U 39).
"OFF", "L" (pilot bulb and rear light) and "H" (main
bulb and rear light) and an additional High/Low beam "Dip/Dipper/Dimmer" switch mounted
on the left hand side of the handlebar. Civilian bikes had a brake light
option as well as a sidecar option. Military machines never had a brake
light based on available diagrams.
Late 1939 (between October 21st, based on latest known original machine
and December) a requirement for a tail light only option was added
requiring some adaptations of the earlier machines.
For this option a 4 position switch, "OFF", "T", "L", "H" was
introduced.
On May 5th 1941, DME Circular B.141 mandated the removal of the Dipper
switch from the existing motorcycles and the fitting of new headlamp masks
(black-out).
Pictorial evidence showed that this ruling was not always followed. Most
likely it was only done during major overhaul or rebuilding of the
bikes.
With the introduction of the black-out mask, there was little use of the
dipper switch arrangement with High/Low beam option. The bulbs were
now double filament, giving a spare filament in the same bulb.
Nearing the end of the war, an "improved" wiring scheme was
introduced, to reduce the number of wires running from the front fork to
the rest of the machine after it was recognised that many electrical
faults developed through chafing, resulting from the continues movement of
the front fork. This system was also introduced on other brand motorcycles
like the BSA M20.
A late wartime Norton maintenance and instructional manual describes a modified
electrical system. This
system consisted of the deletion of the ammeter, and introduction of a push
button in the headlamp panel to change from Pilot to Main bulb and a
"new" switch (U39-L15) mounted at the right hand side under the
saddle. With this configuration there was only one lead left from the
frame to the headlamp.
The instrument panel on top of the headlamp shell was made without aperture for
the ammeter, and a smaller hole to fix the push button.
The
switch had also 4 positions : "Test", "Off", "T" (tail only) and "H" (tail and
headlamp on). The test position connected the D terminal of the dynamo
directly to the tail light. The brilliance of the taillight was then
supposed to be a measure for the operation of the charging
system.
Lamps
were 24W main bulb (double filament), 3W
pilot bulb and 3W tail lamp bulb. The16H and Big 4 the sidelamp and Big 4 axle flood
light were also 3W bulbs.
An "Altette" horn complemented the system where the early bikes
used the HF935 and the later used the HF1235, operated through a horn push
button on the right hand side of the handlebars.
Wiring
diagrams for 16H and Big4 are basically identical apart from the
sidecar light on the pre 1941 Big 4 sidecar combinations and the additional axle flood light
and change over switch on the later Big 4 sidecar combinations.
Note:
It appears that the military machines did not always follow the Lucas given
colour codes for all periods. Up to October 1939 the dipper switch wire
was a combination of red, blue and black wires in one sheath whereas the
Lucas drawings all give 1 blue & white and 2 blue wires in one sheath.
The wire from the switch to "A" of the CVC regulator is coded red &
yellow on early machines and purple & white on the later machines.
The wire from the switch to the tail light is coded red/black on the
earlier machines but coded red on later machines.
Colour codes for the simplified scheme are again slightly different from
the earlier schemes, F CVC to Dynamo became green instead of previous
green black and single wire to headlamp was now only blue.
|
Wires:
On unrestored
remains of a machine from Contract C5109 (1939/1940) the following was
observed:
The wires were tin plated copper wires covered with rubber insulation.
Identification was through coloured rubber sleeves near the terminals.
The dipper switch wire was like a present day 3 lead wire with blue
coloured individual insulated leads combined in one outer cover.
Note:
These early rubber covered wires used tinned copper leads because the
sulphur in the vulcanised rubber leads to oxidation of the copper.
Rubber itself deteriorates through the exposure to oxygen and UV
radiation, becoming very hard and brittle.
For this reason not many original looms still exist.
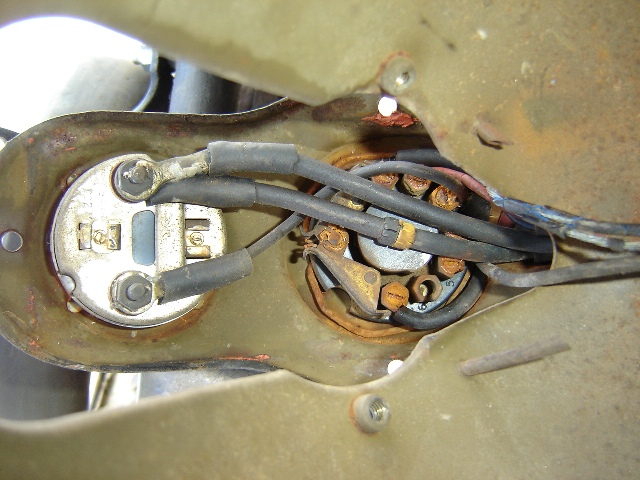
Remains of original wires found on a switch as applied in the late
war electrical system (1944/45) appeared to be rubber like, similar as
described above.
This indicates that rubber encapsulation was used during the entire war.
Picture from article of Steve Madden, courtesy Henk Joore's
WDBSA.nl website.
At least 2 different diameter wires have been found, approximately
Ø
4,6 mm and
Ø
5,7 mm as
measured on the insulation.
Wiring remains on a late-war (re?)built machine showed to have cloth
covered leads. It was not possible to assure this was factory applied.
Whether the use of the cloth encapsulated wire was widespread is difficult
to say. Cloth encapsulated wiring was used on motorcars and
motorcycles in the 20ties and 30ties.
Wiring
harness and
wire fixing
The main wire loom was
protected by a rubber sleeve from the headlamp shell mounted switch
panel through a loop clamp on the right hand side of the front fork, under the upper frame tube
until the saddle tube frame casting. From there on the individual leads went
to the Dynamo, CVC, and tail light. The life horn wire ran parallel to
the wire loom/rubber sleeve from instrument panel directly to the horn.
The horn earth wire ran directly from the horn to the handlebar push
button. The battery earth wire was fixed to the top battery carrier
stud.
Attached pdf "Wiring
harness cable clamps" shows the clamps and positions as best as I have been able
to reconstruct. I do not claim to have it absolutely correct but it
is better than ever seen before, which is nothing!
Batteries and CVC
(Constant Voltage Control)
regulators
It is not exactly known which
battery type was used on the 1936 built machines.
From 1937 onwards, the military machines were provided with a fairly
lumpy "Ni+Fe" (Nickel-Cadmium)
alkaline battery.
These "Ni+Fe" batteries were purchased under the Lucas name "C105 Ni-Fe
battery" but in actual fact produced by the "Batteries Ltd.
Redditch" company.
A more elaborate
description of the Lucas C105 batteries can be found via link
below:
pdf
article on Ni+Fe batteries .
First mention of the "Ni+Fe" type was in the 1937 Norton
production administration and the last use of
it was registered in October 1939.
The "Ni+Fe" alkaline batteries were eventually replaced by the more "normal" Lead
Acid type batteries, primarily the Lucas PUW-5E and equivalents later in
the war. The India Office used the Exide lead acid batteries for all
their machines.
Because of the different charging requirements there were also two types
of MCR1 CVC's. Each clearly marked with either "Ni-Fe" or "Lead Acid"
above the FADE markings. The "Lead Acid" marking was finally deleted around 1941
when the Ni-Fe's were all replaced by Lead Acid batteries and the
distinction was not necessary anymore. Lead Acid batteries could work
with Ni-Fe CVC's but it was only allowed for a short period and not
recommended.
Many
(but not all) Lucas parts are provided with the manufacturing date stamped into them. If
you really want to restore a bike to "factory" fresh condition,
searching for correctly dated Lucas equipment should make your life
exciting.
Actual equipment:
The
Electrical equipment picture page gives some indication on what the
different parts basically look like.
|